Digitally Transform Your Business with Product Lifecycle Management (PLM) Cloud
-
Posted by Harry E Fowler
- Last updated 7/26/19
- Share
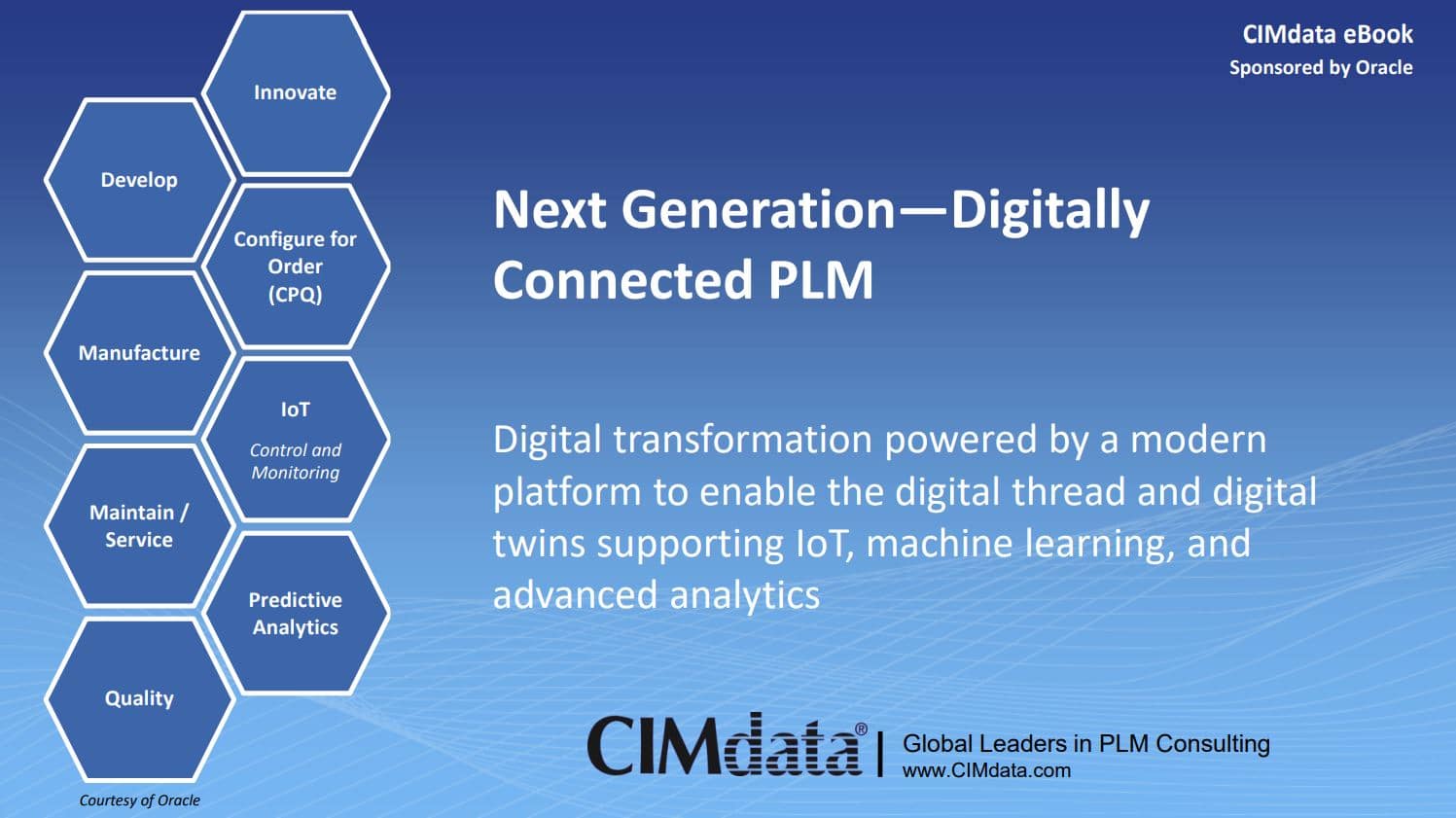
CIMdata, a leading PLM research and analyst firm, recently released an eBook sponsored by Oracle that discussed how to digitally transform your business through Oracle Product Lifecycle Management (PLM) Cloud. The eBook examines the evolution, strategy, and future vision of PLM, how PLM solutions are being rearchitected as product innovation platforms, and how companies can change from designing unsuccessful products to delivering winning offerings.
Key Takeaways
There were five key takeaways identified in the eBook.
- Modern product innovation platforms are making lofty PLM visions and strategies achievable. Legacy PDM tools that struggle to manage CAD files and documents through design and release lifecycle processes can’t support digital transformation, Industry 4.0, and other similar initiatives.
- Digital transformation initiatives must address product definition data to have real business impacts. A complete definition of the digital twin enables what-if scenarios and predictive analytics. The end goal is to reduce risk and continuously improve delivery through all phases of a product lifecycle.
- Connecting quality inspections with operational data via IoT and predictive analytics drives good decisions for closed-loop corrective actions across product, resources, and suppliers.
- The Oracle PLM Cloud solution enables lifecycle processes from concept through commercialization and supports real-time collaboration across supply chains by leveraging data stored within the enterprise product record.
- Oracle PLM Cloud capabilities extend well beyond the product innovation platform and are able to support business platform and digital transformation needs across industries and multiple enterprise software domains.
Introduction: The Evolution of PLM
The creation of CAD software introduced a problem of how to manage, distribute, find, and reuse CAD files. Product Data Management (PDM) was introduced to help tackle this problem and has evolved over the years to support ever-increasing business needs.
Before 1990, PDM solutions were CAD-centric and focused almost entirely on CAD file or document management. This quickly expanded to managing bill of material (BOM) and engineering change processes but remained focused around product development processes and designer and engineer productivity.
In the 1990s, globalization, outsourcing, and time-to-market pressures forced companies to expand their PDM deployments. Early product lifecycle management (PLM) solutions were introduced with robust security and collaboration features, as well as support for many processes and functions throughout the product lifecycle to address challenges beyond core product development. While PDM is still the core of any PLM solution, legacy tools were neither complete nor user-friendly and required expensive and extensive customization.
After 2000s PLM emerged and incorporated more capabilities across the lifecycle including innovation management, requirements management, and improved connections with downstream manufacturing, supply chain processes, and commercialization processes. In many cases, these capabilities were acquired and integrated with legacy tools. While companies were able to leverage this new functionality, it was much more complex and still required extensive customization.
Meanwhile, the pressures that drove the initial development of PDM and early PLM solutions grew. Businesses demanded better solutions to meet their product and process innovation requirements, as well as the latest digital transformation and Industry 4.0 initiatives. In the past few years, the convergence of technologies like Cloud, IoT, Industry 4.0, machine learning, augment and virtual reality (AR/VR), and more, have been enabling companies to transform how they design, manufacture, service, and sell their products.
CIMdata recognized the technology shift and identified how PLM solutions were being rearchitected as product innovation platforms that are able to support today’s digital transformation and Industry 4.0 initiatives. The eBook examines how companies are utilizing PLM to support various digital transformation initiatives and how companies can change from designing unsuccessful products to delivering winning offerings.
The Next Generation of PLM
Traditionally, PLM solutions were toolkits that often required extensive customization to meet business requirements. They were implemented to support an internal, engineering-centric viewpoint. The cost and effort required to get basic capabilities in place within engineering groups meant that initiatives stagnated within the product development department. Product innovation was constrained by the internal walls of the enterprise. This “inside-out” legacy approach focused on part and BOM management, CAD integration, and engineering change management. In the best-case scenario, ERP integration minimal analytics capabilities were also considered in scope.
In today’s fast-paced and customer-centric businesses, leading organizations use analytic, data-driven approaches to anticipate customer needs, leverage supply chains, and ensure customer satisfaction. This “outside-in” approach tightly links the voice of the customer with the voice of the product into the digital twin delivering the visibility necessary for smarter innovation.
Digital Transformation with PLM
Products generate revenue, so improving products and related services by improving product creation processes will generate the value that customers expect and pay for. This is not a new concept, and neither are the pressures on companies to innovate – globalization, regulation, cost, quality expectations, and product complexity. All of these pressures continue to increase over time.
Companies have to be able to calculate and anticipate the changing demands and evolution of their customers. Increasing complexity means that innovations more commonly involve a connected combination of products, software, and services. Meeting customer expectations in the digital age requires fast access to real-time global product data and nimble business operating models.
This fundamental shift in the paradigm provides companies with an opportunity to evolve into a trusted source of business value while increasing collaboration with their customers to feed the innovation cycle. This continuous loop unifies products, services, customers, employees, and partners while helping organizations to deliver ongoing value that creates memorable experiences, enables on-demand fulfillment, and provides personalized services.
The new piece that comes into play is the availability of technology to effectively support digital transformation. Product innovation platforms are able to create, capture, and manage digital twin data. Modern integration technologies enable connections to other platforms, including social platforms so social monitoring can be used to define and refine requirements. IoT can also be used to drive predictive maintenance solutions that leverage exact product configuration data stored within the digital twin. Advanced analytics that leverage machine learning and deep learning are also starting to be used to understand how products are used, which allows product planners to create new features and remove unused ones – closing the loop between the customer and the product developer. In essence, a product innovation platform has become invaluable when customers demand speed of information, cost efficiencies, and exceptional services.
CMIdata believes that product data is at the core of any successful digital transformation.
Digital Transformation Starts with the Digital Thread
Digital transformation requires a connected next-generation PLM solution that supports Industry 4.0. PLM implementations need to extend beyond the traditional product master to “digitally thread” data across the entire product lifecycle and through barriers of siloed information.
The digital thread provides the true foundation for end-to-end connected digital product chains and delivers the traceability that is necessary to quickly track the entire lifecycle of a product from the initial idea and design through commercialization, in-field use, and service.
The graphic below shows how to use a digital thread to link the structures that describe the product over its lifecycle.
Quality is the Key to Successful Products
Digitalizing the quality processes has been a driver to achieving Industry 4.0 initiatives. Quality touches most processes during the lifecycle as the product matures from design to manufacturing through to service. For many companies, each process step represents a data silo that consists of data from disparate systems and sources and analysis assembled with human glue.
With quality management enabled by a product innovation platform, quality planning, control, and compliance processes become a streamlined, collaborative single source of truth that supports capturing, triaging, and managing issues across requirements and part specifications. Quality plans associated with all levels of product configurations define quality inspection requirements and context for IoT data. Connecting requirements configurations and operational data enable predictive analytics. Access to good, real-time quality control data provided by IoT enables early detection of issues and improves responsiveness to resolve closed-loop corrective actions across the full spectrum of products, requirements, resources, and suppliers.
Oracle’s Cloud Approach
Oracle supports the end-to-end, unified business processes that are required by supply chains of the 21st century. Companies that are deploying Oracle ERP Cloud modules are able to consume data directly from the PLM release process into Project Management, Manufacturing, Planning, and Configure Price Quote solutions.
In addition, Oracle has a wide footprint of applications that are built to address Industry 4.0 transformational initiatives, and CIMdata rates Oracle as a PLM Mindshare Leader.
Designed for “plug and play,” Oracle PLM Cloud and SCM Cloud applications deliver modern features like chatbots, embedded social networking, and advanced data visualization.
Oracle PLM Cloud Benefits
Using the Cloud is essential for digital transformation and is the future of product lifecycle management. Some of the key benefits of Oracle PLM Cloud in particular include:
Oracle Cloud is a business platform that is capable of supporting a comprehensive set of information capabilities that are required by today’s modern business – well beyond the scope of PLM. It is a great example of an enterprise business platform approach that can scale to meet the requirements of the largest businesses.
Oracle’s platform technologies that support Oracle PLM Cloud allow product data to be connected to feedback sources across the extended enterprise – from supply chain participants through distribution to the end customer and consumer. The connections implement Oracle’s concept of a “digitally connected PLM” by creating a comprehensive landscape of integrated Cloud applications and harmonized enterprise product record supporting digital twins across the entire product lifecycle.
Oracle PLM Cloud’s “outside-in” approach connects innovation, enterprise quality, analysis, collaboration, social monitoring, and IoT data and processes with product development and change management to supply chain and sales commercialization operations. This combination has a dramatic impact on reducing risks and shrinking new product development lifecycles by sharing data management best practices across the broader supply chain.
To learn more about Oracle SCM Cloud, Oracle PLM Cloud, and more, check out the additional Oracle and Quest resources attached below.